The authors are partners at New York City-based global management consulting firm McKinsey & Co. Opinions are the authors’ own.
On the one hand, prospects are bright for the construction industry. With the global middle class growing fast and the need for all kinds of infrastructure, spending on construction could reach $22 trillion by 2040, up from $13 trillion last year.
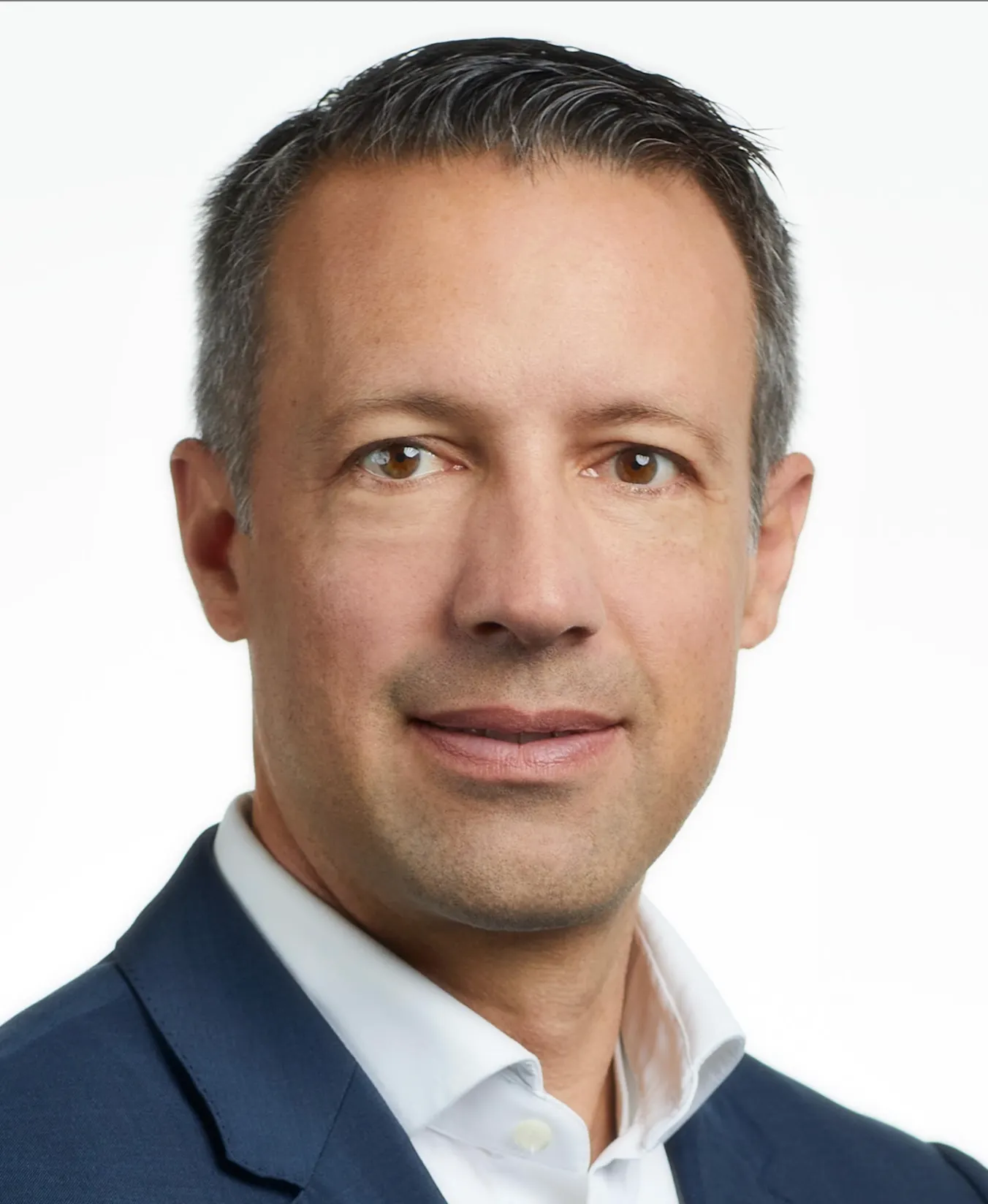
Jan Mischke
Courtesy of McKinsey & Co.
On the other hand, that potential will go unfulfilled if the industry doesn’t step up. For one thing, it will need to almost double its growth rate (outside China), from 1.3% to 2.7%. For another, not only is there already a skilled labor shortage in many markets, but a large cohort of workers is nearing retirement. In the United States, the number of job vacancies in construction doubled between 2017 and 2023.
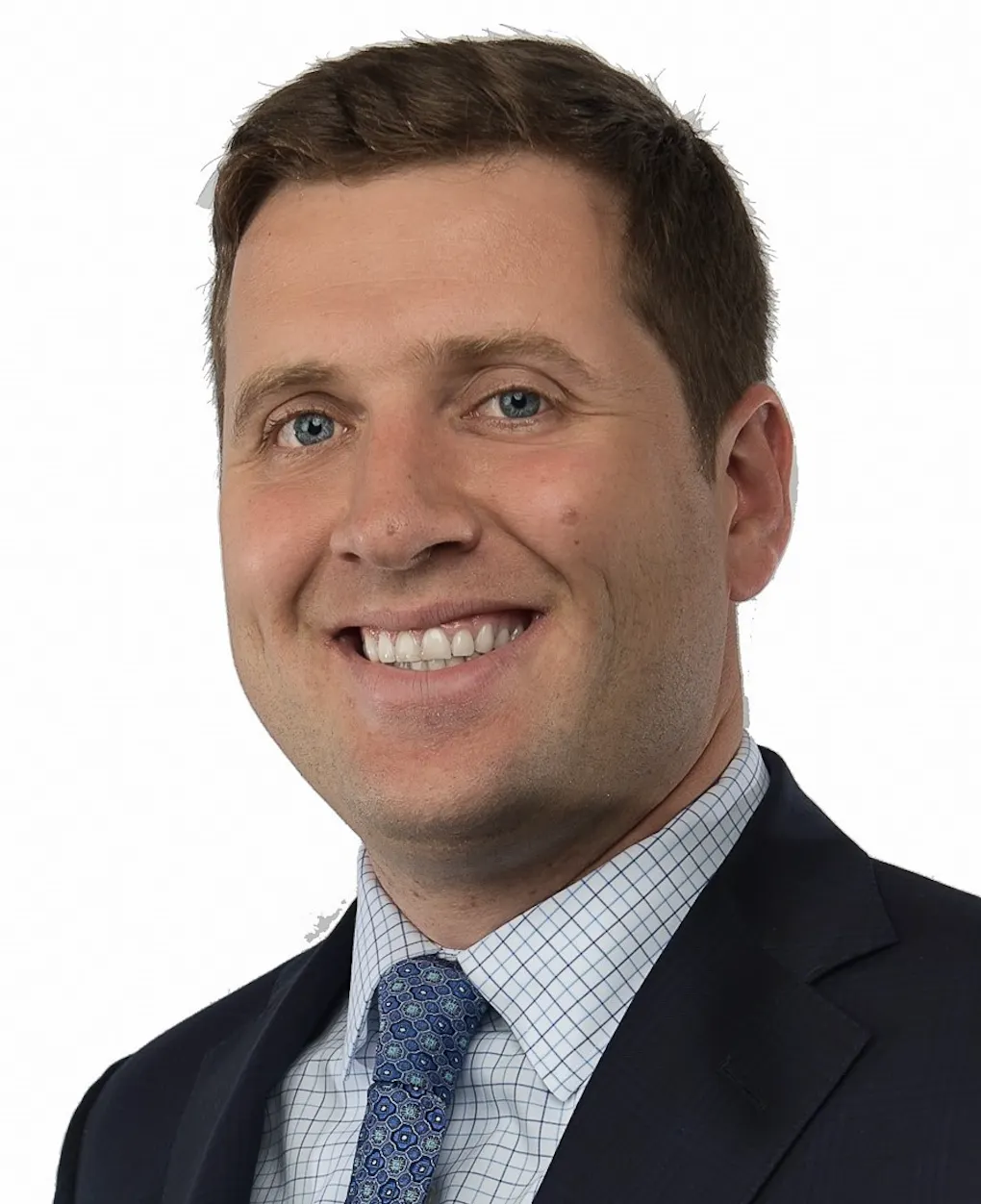
Kevin Stokvis
Courtesy of McKinsey & Co.
Finally and perhaps most important, productivity growth has been poor. Of course, some individual firms have done well. The fact remains, however, that from 2000 to 2022, global construction productivity improved only 10%, just one-fifth the rate of the overall economy.
In advanced economies, such as Europe and the United States, the situation is even worse, with productivity falling since 2000, even as costs have risen faster than inflation. Put it all together and construction output could fall a cumulative $40 trillion short of demand by 2040.
1% per year
That is the problem and if it were easy to solve, it would have been. But that does not mean it is insoluble. If the industry could fill its workforce gaps while improving its productivity by 1% a year, it could go a long way toward addressing that looming $40 trillion shortfall.
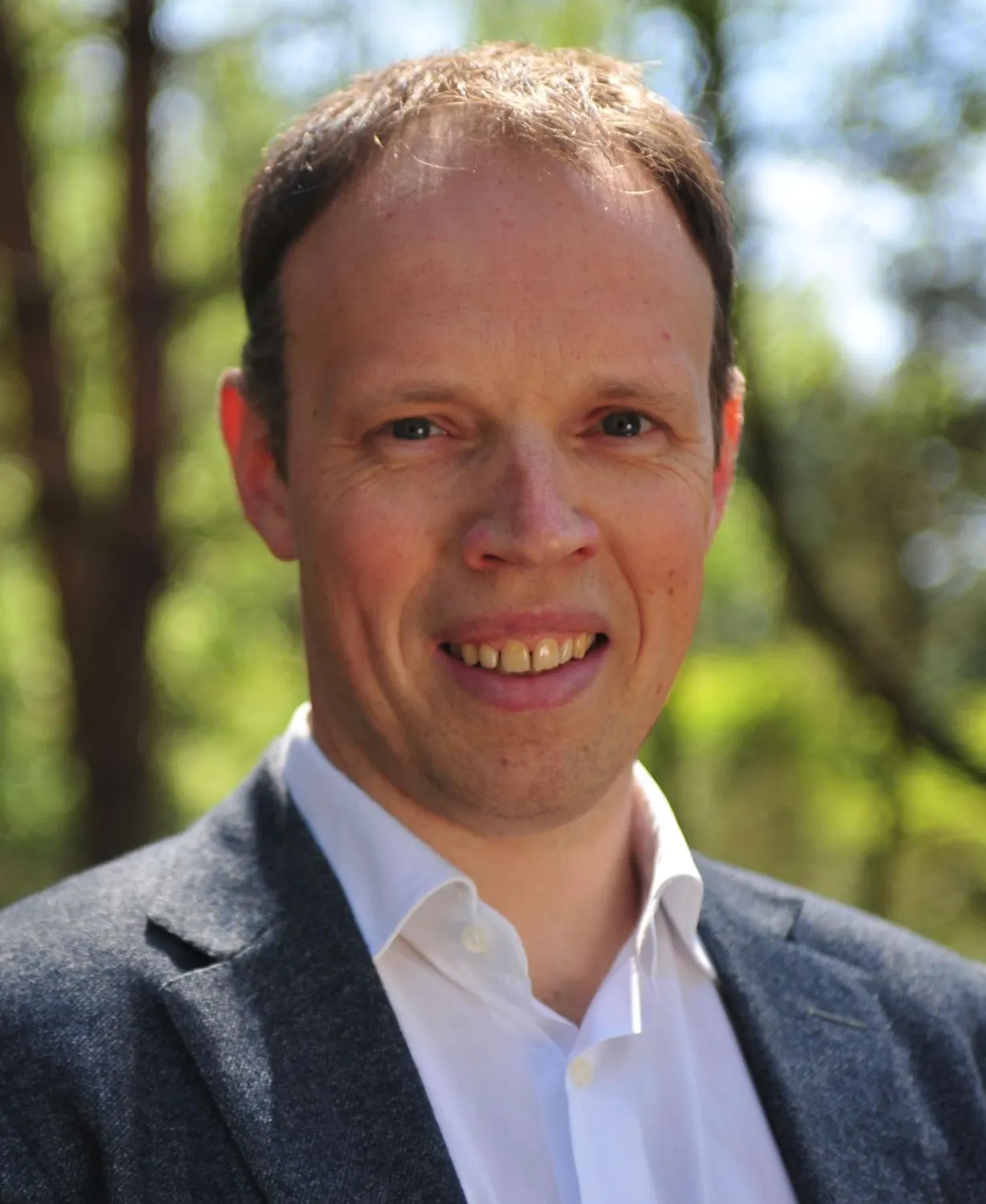
Koen Vermeltfoort
Courtesy of McKinsey & Co.
Those are big ifs. But to a large degree, the solutions are in the industry’s own hands. The lack of standardization in construction design, including slow take-up in the use of modular components, for example, has been a well-known problem for years. Less than 4% of current U.S. housing stock and 15% in Japan has been built using modular techniques.
3 possible solutions
Here are three actions that construction companies can take to boost their productivity.
Embrace upskilling. Companies are often willing to accept a less-skilled or less-experienced workforce for the sake of getting the job done. There is a place for such stopgaps, but it is not a talent strategy.
Research on the impact of temporary employment shows that temporary labor has a damaging effect on productivity. The industry needs to step up skill-building. In addition, it can do a better job constructing attractive career paths for potential workers and fostering mobility for current ones.
Examples include technology-supported learning journeys, apprenticeships and project academies. Partnerships with universities, community colleges and high schools could make young men and women more aware of the possibilities of a career in construction, while helping them develop the skills to succeed. Finally, while there are labor shortages, there are also many people not in the labor force at all. Companies might want to consider overlooked sources of talent.
Nurture a supplier ecosystem. Supplier ecosystems can foster stability, so that owners and partners operate with transparency, credibility and stability. On that basis, construction companies can accelerate learning and improve how they work. Instilling such habits across an ecosystem can build trust and promote positive change. Owners typically set up these partnerships; it is important that they role model the desired way of working.
Reform project management. The traditional project delivery model is characterized by a lack of integrated systems thinking, the prioritization of short-term cost management over long-term outcomes, poor communication, rigid planning systems and tight budgets. All this discourages managers from trying new things that could benefit future projects.
One way to address the problem is for project teams to follow the lead of manufacturing and shift their focus to production rate metrics, such as meters welded, volumes excavated and drawings reviewed. This would allow teams to be more experimental, while also enabling them to spot small problems before they become big ones.
Another is to work with project owners, including governments, to spread risk, particularly in complex projects and particularly when delays are clearly due to matters out of their scope, such as discovery of archaeological remains, endangered species protection or permitting delays. Making outcomes more predictable could be an effective, if indirect way, to boost long-term productivity.
Construction accounts for about 7% of global GDP and 8% of employment. The ripple effects of its difficulties spread far and wide. If the sector does not address its labor and productivity challenges and falls $40 trillion short by 2040, it will mean fewer homes and hospitals, less transport, slower growth and insufficient investment in climate-efficient infrastructure of all kinds. Not to mention a poorer quality of life.
For a traditional, capital-intensive industry like construction, change does not come easy or fast. The point, however, is that for their own sake and for the societies they serve, it is urgent for companies to start.